Unleashing Excellence in Metal Fabrication: The Role of Top Automotive Mold Manufacturers in Modern Industry
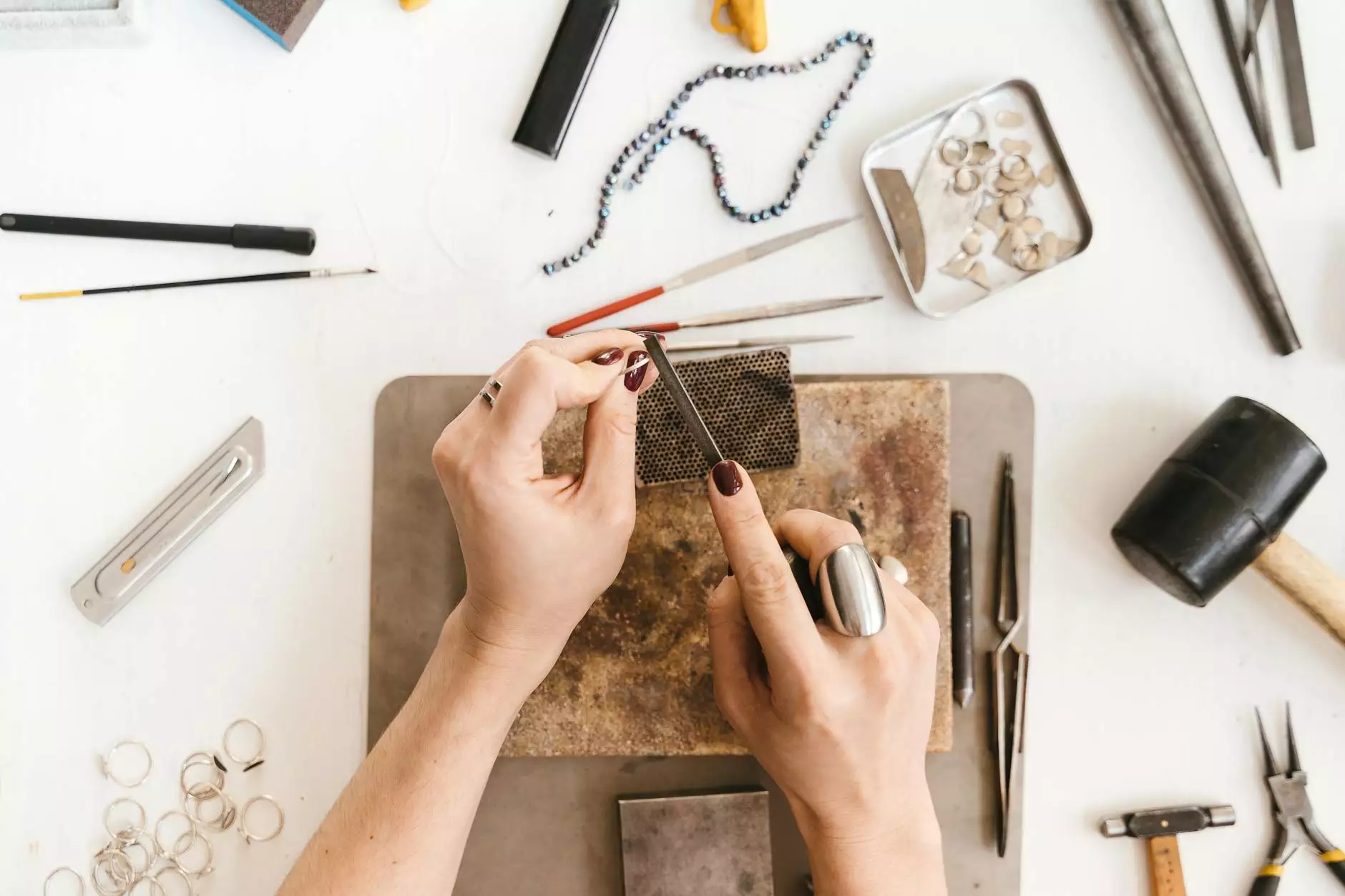
In today’s fast-paced automotive industry, the importance of innovative, durable, and precise molds cannot be overstated. Automotive mold manufacturers stand at the forefront of this technological revolution, playing a critical role in shaping the future of vehicle manufacturing. As a leading metal fabricator specializing in advanced mold solutions, DeepMould has established itself as a cornerstone in the realm of automotive mold manufacturing. This comprehensive guide explores the vital aspects of this industry, emphasizing how top-tier manufacturing translates into superior automotive products and what sets reputable companies like DeepMould apart in this competitive landscape.
The Significance of High-Quality Automotive Molds in Vehicle Production
Automobiles are complex engineering feats that demand precision and consistency. Automotive molds are indispensable tools that facilitate the mass production of vehicle components—ranging from body panels to intricate interior elements. The quality of these molds directly influences the final product's fit, finish, and performance, making them pivotal to manufacturing success.
Why are high-quality molds essential?
- Enhanced Precision: Accurate molds produce parts with tight tolerances, reducing assembly issues.
- Cost Efficiency: Durable molds withstand high-volume production, minimizing downtime and replacement costs.
- Consistent Output: Precision molds ensure uniformity across thousands of parts, maintaining brand integrity.
- Design Flexibility: Advanced molds enable complex geometries and innovative designs.
Innovative Technologies in Automotive Mold Manufacturing
Leading automotive mold manufacturers leverage cutting-edge technologies to meet the rigorous demands of modern vehicle design. These innovations drive improvements in quality, efficiency, and production speed.
1. CNC Machining and 5-Axis Milling
Computer Numerical Control (CNC) machines with 5-axis capabilities allow for highly precise and intricate mold fabrication. They facilitate complex geometries and reduce manual intervention, resulting in faster turnaround times and superior finish quality.
2. CAD/CAM Design Integration
Advanced Computer-Aided Design (CAD) and Computer-Aided Manufacturing (CAM) software enable accurate modeling, simulation, and optimization of molds before manufacturing begins. This integration reduces errors and shortens development cycles.
3. Additive Manufacturing (3D Printing)
For prototyping and complex internal structures, 3D printing technology has become an invaluable tool. It offers rapid iteration capabilities and aids in verifying design feasibility before investing in costly molds.
4. Hard Coatings and Surface Treatments
Modern surface treatment technologies extend mold longevity and improve surface finishes, ensuring high-quality, long-lasting molds capable of withstanding high-pressure injection operations.
Materials and Design Considerations for Superior Automotive Molds
Choosing the right materials and design techniques is vital for manufacturing durable and high-performance automotive molds. The most commonly used materials include high-speed steels, tungsten carbides, aluminum alloys, and specialized composites, each selected based on specific application needs.
Design for Manufacturability (DFM) principles guide mold design to optimize efficiency, minimize material waste, and facilitate ease of maintenance. Emphasizing modularity, symmetry, and standardization allows automotive mold manufacturers to produce versatile solutions that accommodate evolving industry standards.
Surface Finishes and Quality Control in Mold Manufacturing
The aesthetic and functional quality of molded automotive parts hinges on surface finishes, which impact paint adhesion, appearance, and part accuracy. Industry-standard surface treatments such as polishing, texturing, and coating are integral to achieving desired specifications.
Rigorous quality control procedures—including coordinate measuring machines (CMM), dye penetrant testing, and dimensional inspections—are employed throughout the mold manufacturing process. Leading companies like DeepMould prioritize quality assurance to deliver products that meet strict automotive industry standards.
Sustainable Practices in Metal Fabrication and Mold Manufacturing
With increasing emphasis on environmental responsibility, top automotive mold manufacturers incorporate sustainable practices. These include using eco-friendly materials, reducing waste via precision machining, recycling metal scraps, and optimizing energy consumption during manufacturing processes.
DeepMould: A Pioneer in Automotive Mold Manufacturing
DeepMould exemplifies excellence in the field of metal fabricators specializing in automotive molds. With decades of experience, state-of-the-art facilities, and a highly skilled engineering team, DeepMould offers bespoke mold solutions that cater to the demanding needs of the automotive sector.
- Cutting-Edge Technology: Utilizing the latest CNC, EDM, and additive manufacturing methods.
- Customization: Designing molds tailored to specific vehicle models and manufacturing processes.
- Quality Assurance: Implementing strict QC protocols consistent with industry standards.
- Sustainable Manufacturing: Committed to green practices in all operations.
Why Choose DeepMould as Your Automotive Mold Manufacturer?
Partnering with a reputable automotive mold manufacturer like DeepMould offers numerous advantages:
- Exceptional Precision: Ensuring parts fit perfectly and reduce the need for rework.
- Rapid Turnaround: Meeting tight schedules with efficient manufacturing workflows.
- Innovation-Driven Design: Incorporating the latest technological advancements for superior molds.
- Cost-Effective Solutions: Reducing overall production costs through durable, efficient molds.
- Comprehensive Support: Providing end-to-end services from design to delivery and maintenance.
Future Trends in Automotive Mold Manufacturing
The industry is continually evolving, driven by technological advances and changing market demands. Noteworthy future trends include:
- Automation and Smart Manufacturing: Integrating IoT and AI for real-time monitoring and autonomous production processes.
- Sustainable Materials: Development and use of eco-friendly, recyclable mold materials.
- Higher Precision and Complexity: Enabling highly detailed and complex parts through advanced machining techniques.
- Customizable Molds for Electric Vehicles: Adapting molds to new vehicle architectures and battery design components.
Conclusion: Elevating the Automotive Industry with Premier Mold Manufacturing
In summary, the role of automotive mold manufacturers in shaping the future of vehicle production is undeniable. Their commitment to innovation, quality, and sustainability directly impacts the durability, efficiency, and aesthetics of automotive components worldwide. Companies like DeepMould exemplify the pinnacle of metal fabrication expertise, combining cutting-edge technology with industry best practices to deliver molds that meet and exceed client expectations.
By investing in high-quality molds and partnering with proven manufacturers, automotive brands can accelerate their innovation cycles, improve product quality, and meet the evolving demands of consumers and regulators alike. The continuous advancement in automotive mold manufacturing not only transforms vehicle design and production but also contributes substantially to the sustainability and technological progress of the entire automotive industry.
Embrace the future of automotive manufacturing today by selecting the right partner for your mold needs. DeepMould stands ready to deliver excellence in metal fabrication—driving innovation, quality, and success for your automotive projects.