Understanding the Role of High Pressure Pipe Fittings Manufacturers
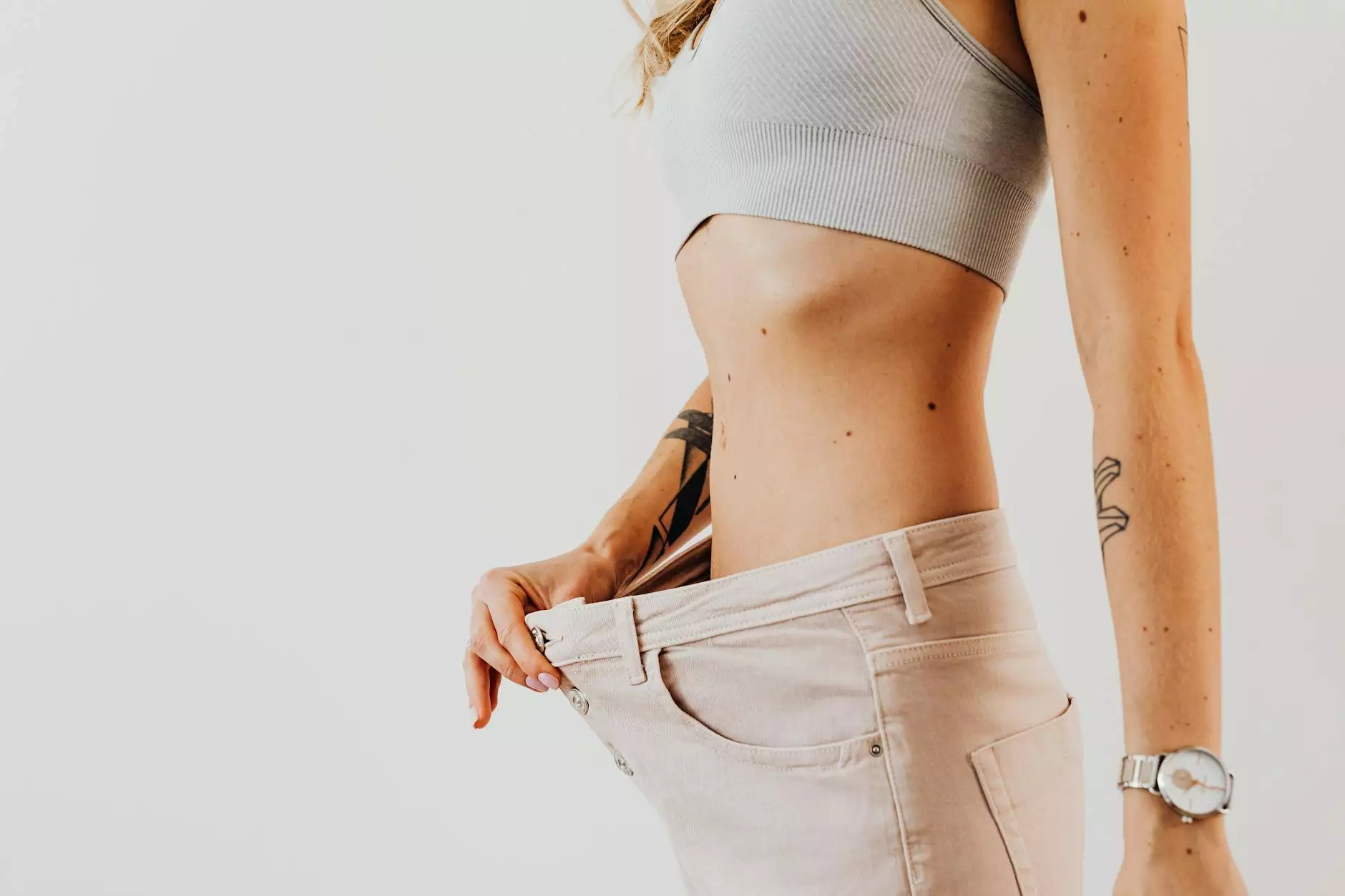
High pressure pipe fittings manufacturers play an essential role in today’s industrial landscape. They produce the fittings that allow pipes to connect, adapt, and alter the flow of fluids under high pressure—critical in numerous industries including oil and gas, chemical processing, and construction. At Samvay Global, we pride ourselves on being a leading name in this sector, committed to delivering exceptional quality and service.
The Significance of High Pressure Pipe Fittings
In any system involving the movement of fluids, the fittings used must withstand specific pressure ratings. High pressure pipe fittings are specially designed to operate in demanding environments. Their importance can be categorized into several key areas:
- Safety: High pressure environments can be hazardous. Properly manufactured fittings ensure the integrity of the system, preventing leaks or bursts that could lead to disastrous outcomes.
- Efficiency: High-quality fittings are essential for maintaining optimal fluid flow, reducing friction losses, and enhancing overall system efficiency.
- Versatility: These fittings can be made from various materials such as stainless steel, brass, or plastic, making them suitable for multiple applications across industries.
Types of High Pressure Pipe Fittings
High pressure pipe fittings come in various types, each designed for specific applications and functionality. Here are some of the most common types:
- Elbows: Used to change the direction of the pipe.
- Tees: Allow branching of two pipes.
- Couplings: Connect two pipes of the same or different diameters.
- Unions: Provide a means to easily connect and disconnect pipes.
- Reducers: Adapt changes in pipe diameters.
At Samvay Global, we manufacture a diverse range of these fittings, ensuring they meet the rigorous demands of our clientele.
Manufacturing Process of High Pressure Pipe Fittings
The manufacturing process of high pressure pipe fittings is meticulous and requires an in-depth understanding of materials, engineering, and the specific requirements of the applications they serve. Here’s how we approach this at Samvay Global:
1. Material Selection
Choosing the right material is vital for the durability and performance of high pressure fittings. Factors such as corrosion resistance, strength, and compatibility with the fluid being transported are crucial. Common materials include:
- Stainless Steel: Ideal for high pressure and corrosive environments.
- Brass: Offers excellent machinability and corrosion resistance.
- Carbon Steel: Provides strength at a lower cost for certain applications.
2. Precision Manufacturing Techniques
Once the materials are selected, the next step involves precision manufacturing techniques such as:
- Forging: Creates a strong, dense material structure.
- Milling: Allows for precise dimensions and tolerances.
- Welding: Essential for forming complex assemblies.
3. Quality Control
Quality control is crucial in our manufacturing process. Every batch undergoes rigorous testing to ensure it meets industry standards and specifications. This includes:
- Pressure Testing: Each fitting is tested under simulated service conditions to verify performance.
- Dimensional Inspection: Ensures that all fittings meet the necessary size and compatibility requirements.
- Material Testing: Verifies that materials conform to the stipulated quality standards.
Applications of High Pressure Pipe Fittings
The applications of high pressure pipe fittings are vast and varied, spanning across multiple industries. Some notable applications include:
1. Oil and Gas Industry
In the oil and gas sector, where high pressure systems are the norm, using reliable fittings is non-negotiable. Our products are designed to withstand extreme conditions, ensuring safe and efficient operations.
2. Chemical Processing
High pressure fittings are regularly utilized in chemical processing plants, where they handle corrosive and hazardous materials. The use of high-grade materials is crucial to minimize the risk of leaks and ensure smooth operations.
3. Marine and Offshore Applications
Marine applications also demand fittings that can resist high pressure and corrosion from saltwater. Our fittings are built to endure harsh marine environments, ensuring longevity and reliability.
Choosing the Right High Pressure Pipe Fittings Manufacturer
When selecting high pressure pipe fittings manufacturers, there are several factors to consider. Here’s a guide to finding the right partner for your needs:
- Experience: Look for a manufacturer with several years in the industry. A proven track record can be a good indicator of reliability.
- Quality Assurance: Investigate their quality control measures. Adherence to international standards like ISO can be a sign of commitment to quality.
- Customization: Does the manufacturer offer custom solutions? Your specific requirements will often dictate the need for tailored products.
- Customer Support: Reliable customer support can make a difference when facing challenges in supply or technical issues.
- Certifications: Check for certifications that demonstrate compliance with industry standards.
At Samvay Global, we excel in all these areas, ensuring our clients receive the very best in high pressure pipe fittings.
Conclusion
As the demand for high pressure systems continues to grow across various industries, the role of high pressure pipe fittings manufacturers becomes increasingly vital. At Samvay Global, we understand the criticality of our products in sustaining efficient operations and ensuring safety.
By focusing on quality, precision manufacturing, and excellent customer service, we have positioned ourselves as a leader in the field. Whether you're looking for valves, fittings, or any other pipe-related products, we are here to meet your needs.
Explore our offerings today and discover why Samvay Global is the trusted choice for high pressure pipe fittings.